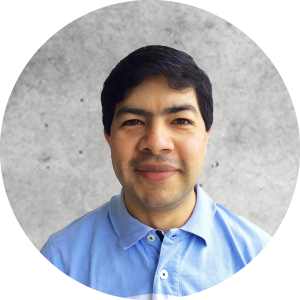
Full time Professor
Bioengineering Department
Volumetric 3D printing is a technique in which a beam of light strikes specific points within a volume of photosensitive resin to activate its polymerisation process, causing these points to solidify and fuse, thus generating three-dimensional structures that form the final manufactured object. This technique is also known as computed axial lithography (CAL) or holography.
Its principle of operation is inspired by the scans made by tomographic scanners, where X-ray beams are emitted from different points of view, which, when intersecting and subsequently processed, allow the three-dimensional architecture of the scanned object/volume of interest to be reconstructed in a three-dimensional model. When this process is carried out in reverse, a three-dimensional digital model is used as a starting point, to which intersecting spatial cutting planes are applied, which become holos or projections, and which are used as opaque sheets to project beams of light onto the photosensitive resin, generating the impression of the model.
Although this technique has an acceptable level of resolution and generates mechanically more homogeneous structures with a better surface finish by reducing anisotropy and the marks generated by the deposition of the material in the form of layers, it has the limitation of not completely controlling the surface geometry, the resolution and the mechanical property of the printed model, due to the fact that the same point of the resin and its surroundings can be exposed to more than one light exposure, generating volumes with heterogeneous levels of polymerisation.
As a new generation technique that eliminates these limitations, the company Xolo® (Berlin, Germany) created Xolography, an improved technique of three-dimensional volumetric printing, in which not one, but two beams of light are responsible for activating the polymerisation process of the photosensitive resin and consolidating or not the solidification of the resin.
The key factor in xolography originates in the nature of the resin and the way in which it is light-cured. The resin has a photosensitive activator that controls the sintering process and requires the superposition of two light beams (with two different wavelengths) to consolidate its photopolymerisation and solidification process at the point (voxel) where the light beams intersect. If a point (or voxel) of the resin receives only one beam of light, its photoinitiator will not be activated and the resin will remain in a liquid state.
In xolography, the resin with which the model will be printed is placed in a small transparent vat, in turn placed on a mobile base with horizontal displacement (figure 1). Through this vat (and the resin inside it) a first beam of light is projected, with wavelength λ1, forming a spatial plane on which a second beam of light, with wavelength λ2, will be projected in an orthogonal direction to the plane of light created by the first beam. Only the resin located at those points (voxels) where the two applied light beams (λ1 + λ2) overlap will cure and solidify (figure 1).
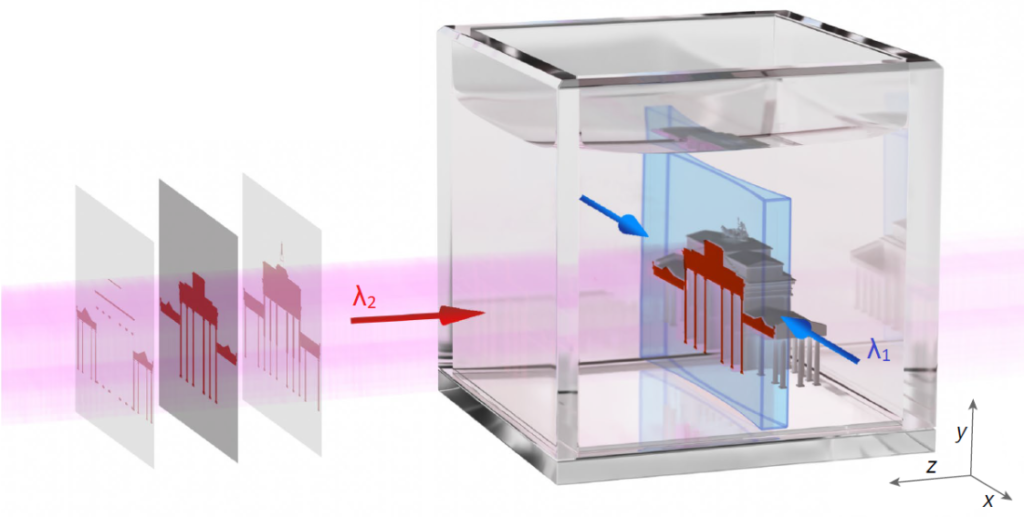
vat. Adapted from [1].
Models printed with this technique achieve excellent surface finish, resolution (up to 25 µm), functionality and mechanical stability (figure 2).
This newly developed technique has enormous advantages over more traditional 3D (bio)printing techniques, such as the fact that it does not print by building up layer upon layer, eliminating the implications that such a form of material deposition entails (mainly anisotropy, uneven or marked finishes, and irregular curing).
Moreover, it has advantages of its own that make it a superior technique for bioprinting, such as: (i) the fact of working with resins whose properties are widely adjustable to the need of the required model, managing to obtain models with optimal mechanical properties according to demand; (ii) by working with light beams, its printing speed is high; (iii) the spatial planes of intersection can be in any spatial orientation, allowing the printing of complex shapes with very high resolution, given that this technique guarantees that each sintered voxel of the resin will be cured only once in each printing process; iv) due to its speed and low invasive effect, it is a very appropriate technique to create scaffolds with cell-loaded resins, preserving cell viability; and, v) due to the viscosity of the resins and the speed of the process, it can print internal and external structures (such as independent mechanisms or microfluidic devices), even eliminating the need to use supports on the model, where other techniques would usually require it.
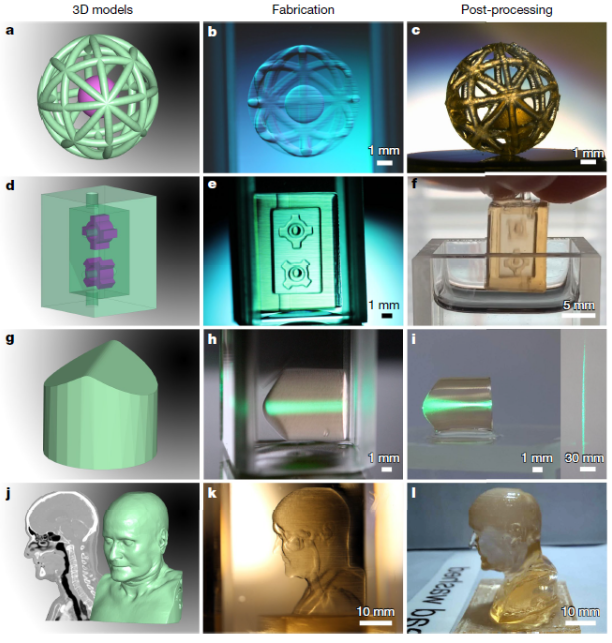
However, the main limitation of this technique is the need to use completely transparent resins that allow the free flow of light beams.
In conclusion, xolography is a cutting-edge (bio)printing technique with great potential to generate solutions for industry and medicine.
Reference:
[1] Regehly, M., Garmshausen, Y., Reuter, M. et al. Xolography for linear volumetric 3D
printing. Nature 588, 620–624 (2020).